Butler Paper Recycling
Thinking Outside the Box
SHARE
Just talk with James “Jay” E. Butler III, fourth generation president of Butler Paper Recycling, Inc., the family business his great-grandfather started as a box manufacturer in 1915, and you may never look at another Amazon delivery in quite the same way.
Today, Butler Paper Recycling is a full-service industrial and commercial recycler of paper fiber and plastic headquartered in Suffolk, with a second plant in Franklin. The company has a hauling business, complete with 10 tractor trailers that pick up and deliver product within 100 miles of the plant, and a brokerage division that buys materials from curbside recyclers and ships it to global markets like Europe and Asia, where there is a shortage of wood and wood fiber. The company has grown and evolved into one of the largest privately held wastepaper recycling companies on the east coast, without losing sight of its origin.
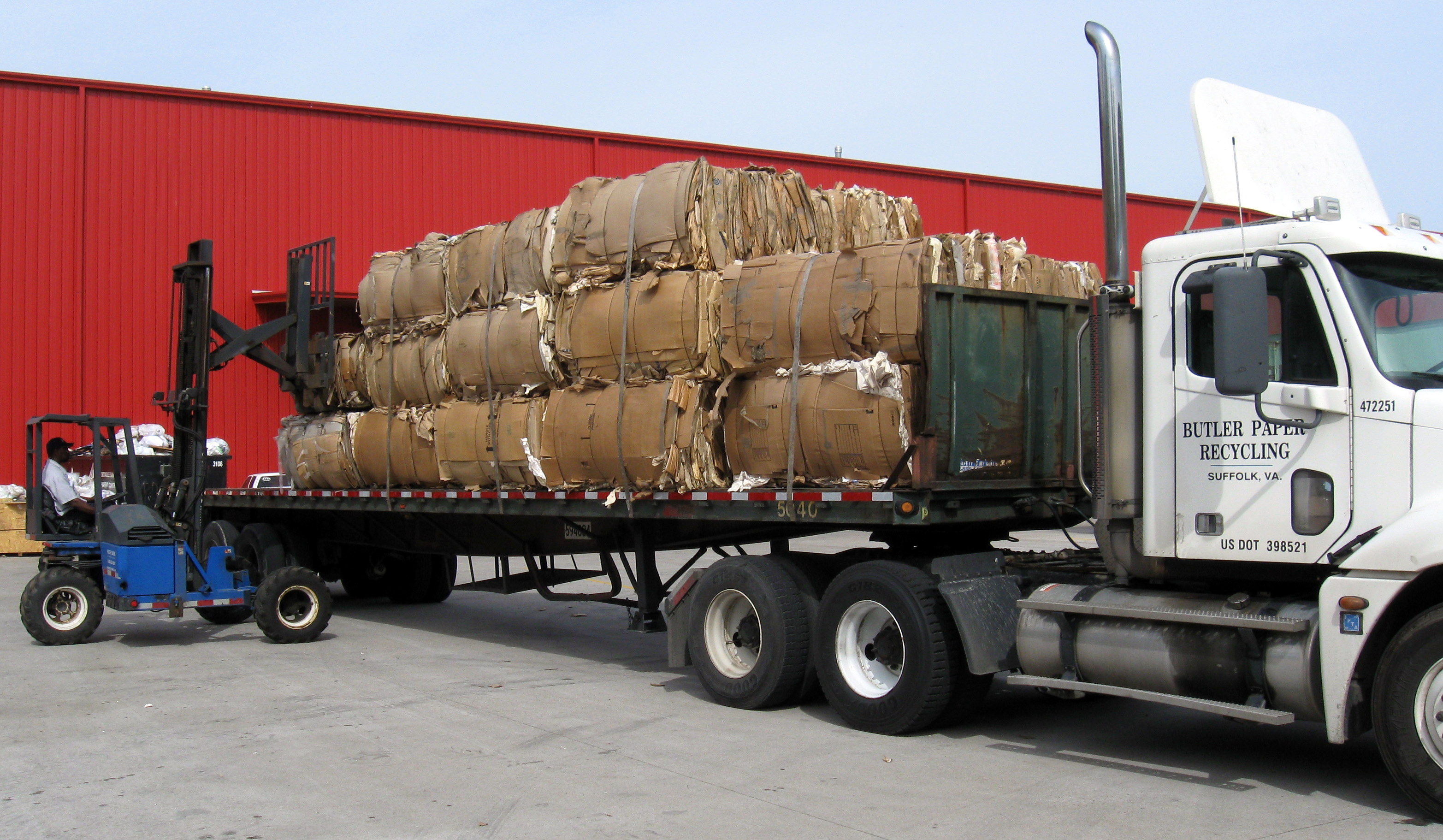
Jay describes its humble beginnings, “My great-grandfather founded the company as a box-making plant for a hosiery mill in Portsmouth, and his son, who was my grandfather, worked for him at the box plant. They got a contract to make candy boxes for Planters Peanuts, so they bought equipment and set up the company in Suffolk. Planters used to make a tray of chocolate covered nuts that was pretty popular. My grandfather ran the company, and we manufactured candy boxes and also gift boxes. We made boxes for Planters for 60 years into the 1970s.”
The Butler family took the old expression waste not, want not to heart. “We always had scrap from making the boxes and we’d carry the scrap back to the paper mill to be recycled, buy the board for making the new boxes, and come back. My father’s first job was baling the scrap at the plant, so he got interested in finding more scrap and more paper to be recycled and carried back to the mill. Over the years, we evolved into being in the wastepaper recycling business,” says Jay.
Jay worked for the company as a laborer when he was in his teens and during his summer breaks from Elon College, where he studied business administration. He took the helm in 1991 when his father retired. His oldest of two daughters, Jenna Butler, followed suit and has worked at the company for 20 years handling human resources.
Jay has seen his share of business challenges. “We are an industrial and commercial recycling company, so our customers are distribution centers, factories, printers, paper mills, and tissue mills. We face the same challenges as anybody in business. It’s all supply and demand so we have to be really good at what we do. We have to be lean because sometimes commodity prices come down and expenses go up, and you have to be able to maneuver through those situations. It’s a real entrepreneurial business. We’ve grown over the years because businesses are making more of an effort to recycle their waste.”
Butler Paper connected with TowneBank in 2000 because they wanted to stay with a local bank. Jay explains, “We like doing business with local people. I like the fact that my private banker Betsy Totten lives in my neighborhood and grew up with my kids. We’re a relationship company. We feel that we have good strong relationships with all of our customers, and we like to have strong relationships with our bankers too. When you know their character, when you know where they came from, it just means a lot.”
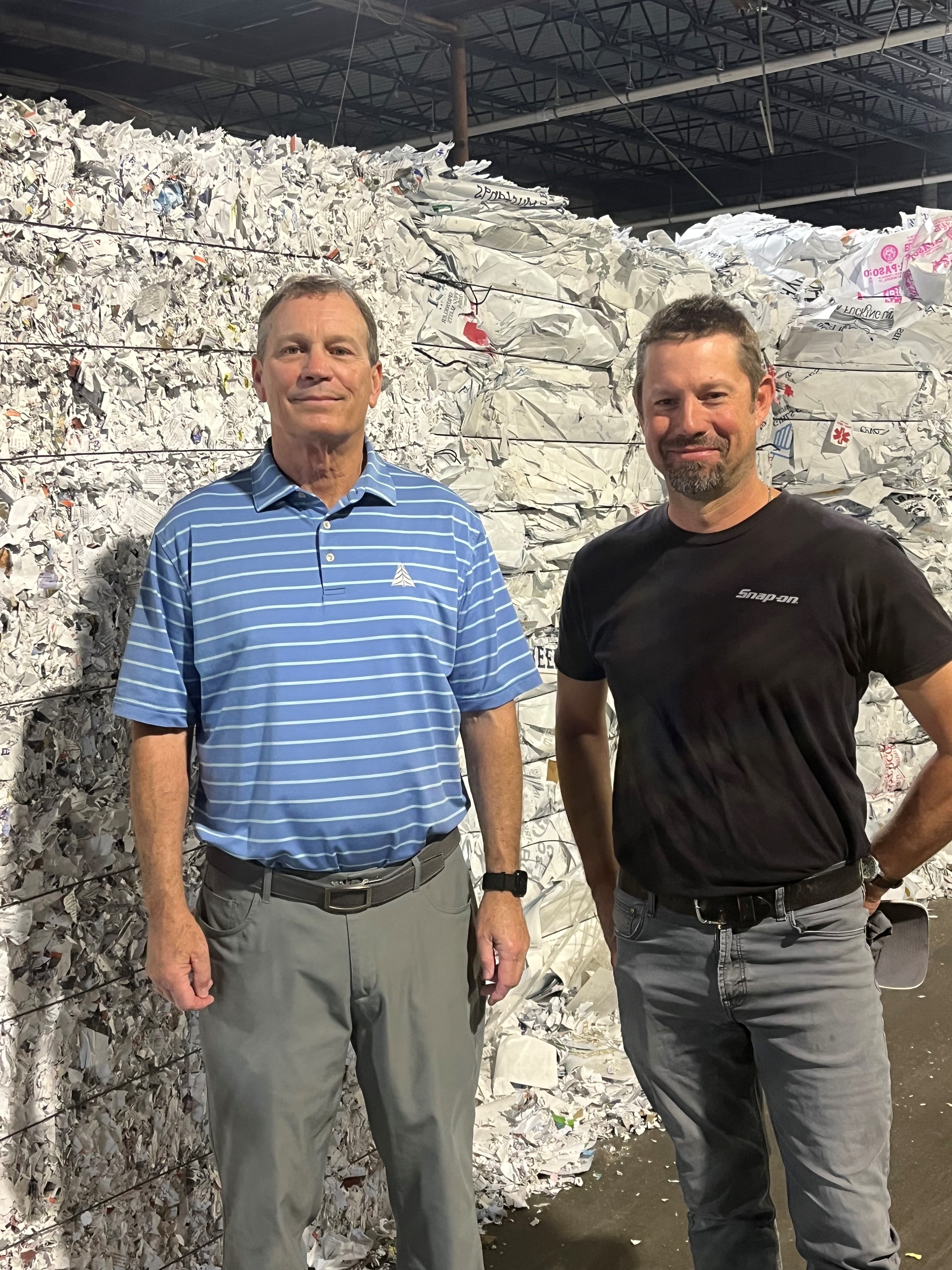
Betsy agrees, “As a community banker, there’s a high responsibility to be there for your neighbor and not let them down from a customer service standpoint. Jay knows he has that working with me at Towne.”
Betsy says Jay is very humble about his business. “From my perspective, they provide a benefit to society as a whole. With so many corrugated brown boxes arriving on doorsteps daily and the global shipping industry expanding every year, this company is brokering, collecting, and sending that product and other recyclables to vendors and companies who can recycle and reuse them. He doesn’t think they do anything special,” Betsy adds, “But I find their work and industry to be pretty fascinating and globally impactful.”
Jay shares his enthusiasm about the history of recycling. “People don’t realize that paper recycling has been going on since the 1800s. You know the gray board on the back of a legal pad or what they make a shoe box out of? It’s made out of materials that have been recycled for over one hundred years. It’s grey in color because it has a lot of recycled newspaper in it.”
While Butler Paper’s mission has changed and expanded over the years, the importance of their starting point – the box – remains. Due to the increase in e-commerce, the demand for boxes and the materials they’re made of has skyrocketed.
“With the Amazon effect, the demand for corrugated boxes is mind-boggling. You used to go to the store and buy one item. Now, Amazon gets a case of those items and has to purchase a box for every item in that case to ship it to you. The demand for fiber to manufacture those corrugated boxes worldwide is astronomical.”
Jay says he has been blessed with a dedicated team of employees and very little turnover. “We have about 45 employees, and 70 percent of our people have been here for 20 years or more. Chris Case is my right-hand guy, he has been with us for 25 years. He is our operations manager and a stockholder in the company. We just have a really great team.”
For more information on Butler Paper Recycling, Inc., visit ButlerPaper.com.